Shine Like the Sun:
Chapter 2: Methodology
INTRODUCTION
As explained in the Introduction, three problematic areas for the study of Islamic pottery have been addressed, specifically concerning chronology, provenance, and technology. To approach the problems of chronology, a corpus of material was assembled and studied, and then developed into a seriated typology. With reference to excavated stratigraphies and other datable material a tentative absolute chronology was developed. After initial investigation of ceramic bodies with the aid of a 10× lens, petrographic analysis was used to group wares by their petrographically defined fabric (petrofabric). Where possible these petrofabrics were attributed to centres of manufacture. Investigation of the technology of glazes, bodies, and to some extent colorants, was undertaken by application of a scanning electron microscope (SEM) with attached analytical facilities.
TYPOLOGY AND CHRONOLOGY
The corpus of pottery assembled for this study consisted of sherds from excavations and surface collection, and unattributed but diagnostic whole vessels. Published material has also been included where possible. The first-hand study predominantly relied upon the sherd and object collections of the Royal Ontario Museum, Toronto (ROM); the Ashmolean Museum, Oxford; the Metropolitan Museum of Art, New York (MMA); and the British Museum, London (BM). Other collections were also studied and incorporated, including those available from publication, but less extensively (see Appendix A).
The pottery has been classified in a hierarchical taxonomic structure, the coarsest division being the Class, which is divided into Types, which is in turn divided into Styles (see Table 2.1).Class is essentially defined by surface technology (slips, glaze), including Opaque-glazed, Turquoise-glazed, and so on. Although these terms often appear general, they are based on obvious differences in appearance supported by distinctions in microstructure and chemistry. Type is defined by the method of decoration (e.g., lustre, underglaze, slip-incised). Style is defined by a combination of vessel form and the styles of decoration, usually expressed as an assemblage of motifs. This system of classification does not always work, for example, Iranian lustre- painted wares may be found on any type of glaze. However, for the bulk of wares it greatly facilitates the study.
Form was studied by reference to whole vessels studied in person, or to published examples with drawn profiles, or by examination of sherds. This latter group was at times the most significant because of the much larger sample size available. Open forms, particularly bowls, are the most common shape in this corpus, so particular attention was given to rim and base profile (see Fig. 2.1) as well as to general vessel form (see Fig. 2.2). Each type of rim or base was defined by a very specific geometry. In similar studies such closely defined characters may be given alphanumeric designations which are usually only remembered by the person doing the study. In this study each particular type of rim or base was given a specific name, which is intended to be evocative of the profile. For instance, "tortoise" and "camel" rims have profiles reminiscent of the relevant beasts. Once these profiles have been seen, it is hoped that the evocative terms will enable the reader to recognize them.
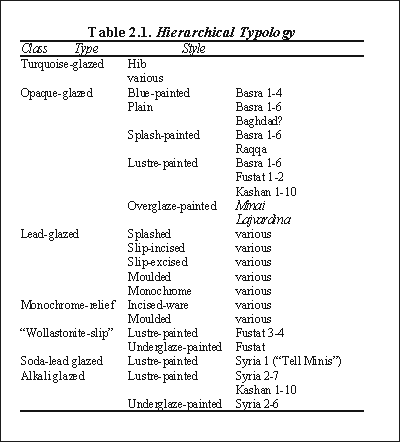
Decoration was analysed by reference to design elements rather than to overall effect. Particular weight was given to those motifs and design elements that were essentially structural, repetitive, and common. These were thought to represent expressions to which the painter gave little thought, being more concerned with the overall effect of the piece.
Once these design elements were identified, their occurrence within a type was tabulated together with vessel form, and was thus subjected to seriation (e.g., Tables 3.1, 3.2). Seriation has been used by archaeologists since its first development by Flinders Petrie (1920:3-6). In Petrie's original work an assemblage of pottery from a tomb was considered as the unit, and the individual vessels were considered the attributes of that unit. Petrie worked out his seriation by creating long cards with vessels drawn on them. He laid the cards out, juggling them around until a sequence could be discerned of individual vessels coming in and then leaving the assemblages. Petrie's early work still stands to this day (Drower 1985:252), and the methodology is the basis of archaeological pottery dating used by archaeologists around the world.
Seriation was applied in the present study by considering the individual vessel as the unit, and the motifs and form to be the attributes. These attributes were correlated in an assemblage of design elements and forms. This assemblage defined a group of pottery with the same Style. At times a style group was distinct from others, with few or no motifs held in common with other assemblages. At other times individual motifs crossed over from one assemblage to another in an interrelated sequence of motif assemblages (i.e., they are seriated). In some circumstances the cause of such stylistic divisions may represent distinct, perhaps contemporary, workshops. In the majority of cases each stylistic group within a type represents a progressive series of developments, which may be best explained by chronologically successive groups. This may be seen in the relevant table (e.g., Tables 3.1, 3.2) where the assemblage shifts to the right down the table, in what is considered to approximate a chronological progression. Also the form studies generally show a continuous line of development (e.g., Figs. 3.7, 3.10, and 3.11), even with an eye to the realities of potting precision (cf. Miller 1985, fig. 9).
This amount of attention was applied only to lustre-painted and related high-quality ceramics (e.g., Iraqi Blue-painted, Iranian Mina'i ware, Syrian Underglaze-painted wares), as this group represented a continuous tradition throughout the period covered in this study. Although it may be possible to refine the chronology by increasing the size of the corpus studied, it was considered a more worthwhile task to cover a greater timespan. For the other classes of wares typology and dating were attempted by reference to the studies for the "finer" wares, and by reference to archaeological association.
PETROGRAPHIC ANALYSIS
Petrographic analysis of pottery has long been a component of archaeological ceramic studies in many parts of the world, with regular application from the sixties onwards. Williams (1983) gives a useful history of the study of pottery in thin-section, with numerous examples of previous studies. Effectively the technique has been used intermittently since its development in the last century, but with continuing application in the US since the work of Anna Shepherd in the forties, in Germany since the fifties, and in Britain and the former Soviet Union since the sixties. Research has covered most periods and regions of the New World, prehistoric to classical Europe and the Near East, and medieval Europe. One of the few areas to have received limited attention in the past is medieval Near Eastern, or Islamic, pottery. Apart from the work of the present author (see bibliography), other published studies of Islamic pottery incorporating petrology have had a distinctively Maghrebi accent, and include those on North African wares (Riley 1979, 1982; Williams 1981; Mannoni 1982) and Spain (Mannoni 1982; Vince 1982; Blake et al., 1992). Ceramic petrography seems to have appeared rather revolutionary to some Islamicists because of their lack of exposure to the technique, but it must be recognized that the technique is regarded as standard, and indeed essential, research by many archaeologists. The objective of most of these studies is largely the same as that of this study. Initially, the objective is to group ceramics together on the basis of their common use of the same raw materials, and to attribute that particular group if possible to a specific site of production. Such studies are especially important in the study of trade ceramics, such as Roman amphorae (Peacock and Williams 1986).
One major difference between this study and those undertaken on other types of pottery, is that much of the material here consists of the quartzose stonepaste type of ceramic body, whereas all other studies have been on clay bodies. For differentiating between groups of stonepaste it has been necessary to develop new criteria for distinguishing the characteristics of each centre.
Procedure
Prior to petrographic analysis, freshly broken sections of the bodies of the corpus of pottery were examined with the aid of a 10x hand lens or a 10× to 40× zoom binocular microscope, in order to separate the material into preliminary groups. The petrographic sampling strategy is based upon this preliminary study, so that each petrographic sample is representative of a much larger group. After petrographic analysis, the material is reconsidered, and macroscopic descriptions are developed for the petrofabrics.
Petrographic analysis itself is a technique originally developed in the earth sciences. It entails taking a sample and then grinding and polishing one side optically flat. This surface is then fixed to a glass slide and the rest of the sample is cut off and ground down so that a section 0.03 mm thick remains on the slide (see Fig. 2.3). This is a thin-section. The sample is now thin enough so that most materials (excluding metals, most metal oxides, sulphides and some other minerals collectively known as "opaques") are transparent. The thin-section is then observed through a petrographic microscope fitted with a number of optical aids, including polarizing filters. These aids enable identification of the mineralogy of the rocks and minerals included in the sample. Various other observations can be made on the texture and relationships of the rocks and minerals, the degree of roundness or angularity of the grains, the sortedness, and the variation in grain-sizes.
Ceramics in thin-section
This technique works with pottery because the ceramic body contains inclusions of rocks and minerals, and analysis of these inclusions provides the basis for defining the "petrofabric" of the sampled piece. This is true both for ordinary clay-based ceramics, and for the siliceous stonepaste body found in Islamic pottery. In the case of clay-based ceramics the inclusions are known as "aplastics" to differentiate from the "plastic" clay minerals. Aplastics are necessary to reduce shrinking during drying and firing, and to prevent various other problems that would occur with a ceramic consisting entirely of clay minerals. In some cases the pottery is "tempered," by having aplastics added deliberately by the potter.
Stonepaste, an important type of ceramic body found in Islamic pottery, is also known as "quartz-frit," "fritware," "faience," "artificial paste," and "kashi." Of all these terms, stonepaste is preferable as it is derived from the Persian name for this material (Wulff 1966); it is also technically the most acceptable. For instance "quartz-frit" and "fritware" are unsuitable terms for this material as it does not actually include frit; neither is it significantly more "artificial" than some clay ceramics. Recipes for stonepaste are available from a number of sources. These include ethnographic studies of recent potters (Wulff 1966; Centlivres-Demont 1971), and two technical treatises, one by Ustad Ali Mohammad, dating to the 1880s (Mohammad 1904), and the other by Abu ‘l-Qasim, dating to about 1300 (Allan 1973a). The stonepaste mixture as described in these sources comprises about eight to ten parts quartz, one part crushed glass, and one part fine white clay. The clay keeps the material together during forming, and combines with the glass during firing to cement the quartz grains together. This mixture varied during different phases in the development of stonepaste (Mason and Tite 1994a, and below), and also differed at certain centres (Tite 1989), but this description is sufficient for our current purposes.
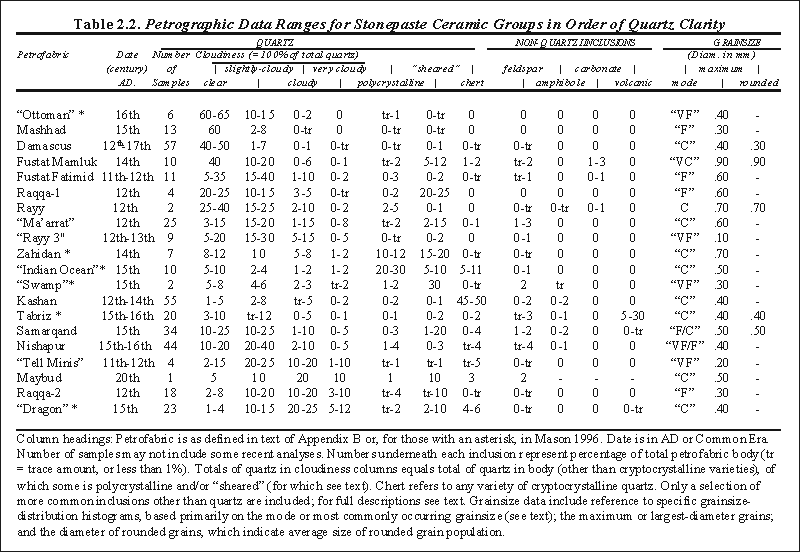
This simple description of the body as comprising quartz, glass, and a little clay provides a challenge to any form of physical characterization. Attempts at chemical analysis are theoretically problematic as the quartz is generally not chemically diverse, the glass is almost entirely dependent on technological determinants for its attributes, and the clay forms a limited component of the final body. The often highly porous nature of the stonepaste body also makes it particularly susceptible to post-depositional changes, while the SEM study has shown that glazes often invade areas of the body, taking colorants with them. Preliminary results, insufficiently advanced to be reported here, of an instrumental neutron activation analysis study by this author of stonepaste ceramics already grouped by petrographic analysis appear to support such pessimism, with even wasters from the same site being separated into different groups.
Similarly, the descriptions of crushed quartz as the sole mineralogical component would theoretically suggest that stonepaste is particularly unamenable to mineralogical differentiation. However, the successful application of ceramic petrography has been made possible through the development of a set of criteria for differentiation of quartz-rich bodies, and this development is the chief methodological contribution of this part of the study. In thin-section a typical stonepaste appears to comprise a substantial content of aplastic inclusions, commonly over 60% of total thin-section. These grains are held together by a glass, which at times appears as a vesicular matrix, and at other times as a tenuous network. An important inclusion to recognize is relict grains of the glass additive. This is not because they are necessarily useful for provenance determination as they are not a geographically determined variable. These commonly form the shape of angular glassy shards and are easily recognized by a rim of high-relief minerals crystallized from the glass during firing (see Mason and Tite 1994a). With increasing temperature the glass phase of the relict glass additive inclusion is lost to the body matrix, and eventually all that is left is the rim of fine crystals. At the highest temperatures this may be expressed solely as a rim of crystals around a bloated pore. Although this degree of destruction is probably related to temperature, there is little feasibility of using this phenomenon to provide estimates of firing temperatures. So many other variables are involved, such as the original chemistry of the inclusion in relation to the local and general chemistry of the body, that it would likely be impossible to determine an absolute temperature to any significantly reliable degree. In August 1996 I visited former stonepaste potters in Shareza near Isfahan and at Natanz, Iran, and they stated that their pottery was fired twice, at 800 C and 1000 C at Shahreza and twice at 1000 C at Natanz.
Mineral abundance
The relative abundance of each mineral or mineral variety is expressed as a total percentage of the body. This value is obtained by comparison with special charts (Terry and Chillingar 1955). This process can be very rapid and is also considerably more informative to non-petrographers than simple word descriptions such as "abundant," "scarce," and so on, which may have no defined limits. Although effectively subjective, and prone to certain optical effects, I have found it sufficiently accurate for this material, and repeated analyses of the same section (whether deliberate testing or accidental re-analysis) have produced effectively the same results. A more precise and accurate technique used by geologists is point counting, in which the sample is moved at a set increment relative to the size of the grains and the mineral at the centre of the field of view (under the cross-hairs) is identified and recorded. For statistically valid samples geologists may take one thousand counts, although some ceramic petrologists have used lesser counts, the statistical validity of which must be questioned. For ceramics with a lot of clay groundmass there may not be a thousand grains to count. Further, the wide variation in grainsize, often mixed by processing and unsorted by natural process, makes it difficult to calculate the appropriate count interval (Freestone 1991a). Other techniques of more accurate and precise determination of mineral abundance may be applicable to archaeological ceramics, but to my knowledge no one has spent the time to determine if they are genuinely applicable to ceramics (such as was done for grainsize distribution recording methods by Andrew Middleton and colleagues, for which see below). Use of comparison charts is recognized as being scientifically credible by geologists, who are the arbiters of methodological rigour in this matter.
The aplastic inclusions of fired-clay ceramics can contain any combination of various minerals and rock inclusions, whereas the stonepaste fabrics must by definition be primarily composed of grains of quartz. A selected range of inclusions has been chosen for the tabulated data, in order to maintain uniformity and thus facilitate comparison. In some cases inclusions which provide important separations between otherwise similar groups are left off the tables or included under other headings (felsic to ultrabasic volcanics under "volcanics" for instance). Otherwise the table would rapidly become extremely wide as well as overwhelmed by dashes which indicate absence of the particular inclusion. In these cases it is important to follow the text closely and to consult Appendix B for full petrofabric descriptions.
Quartz
This abundant mineral is commonly found in nature as either macrocrystalline quartz or microcrystalline/cryptocrystalline varieties. Microcrystalline quartz includes some with granular microstructures (e.g., jasper), and others with fibrous microstructures (e.g., chalcedony, agate, and chert). The petrofabric attributed to Kashan, a very important centre in the twelfth and thirteenth centuries, is characterized by a high content of chert (see Table 2.2 and Chapter 6). Agate is characterized by fine banding which may at times include bands of macrocrystalline phases (although atypical, I have observed this in agates from the Yemen). A group of ceramics from the beginning of the fifteenth century which are found at various sites around the Indian Ocean, including Kisimani Mafia in East Africa and Siraf in Iran ("Indian Ocean" Petrofabric, see Table 2.2), contain grains that exhibit banding of this atypical microcrystalline/macrocrystalline nature. If this banded quartz is indeed fragments of agate in the pottery, then among the regions technically capable of producing this pottery, the constraints of geological predominance (i.e., widespread basalt flows) indicate the most likely production centre for this ware to be around Diyarbakir, in southern Turkey (Mason 1996).
Greater differentiation between different varieties of quartz has not been common practice among ceramic petrographers, although sedimentologists have recognized certain major divisions (Folk 1980:69-81), including polycrystalline quartz grains, which may be fragments of metamorphosed sandstones (quartzite), or may have recrystallized after metamorphic stress (e.g., mylonite). Generally, assumption of genetic origin is avoided unless the evidence is obvious, and polycrystalline grains will be described as having equant crystals (quartzite, gneiss) or elongate crystals (schist). The petrofabric attributed to Nishapur by analysis of wasters of the fifteenth century, when Nishapur was the premier Iranian production centre, often has polycrystalline grains (see Table 2.2; cf. Mason 1996). The source of quartz for the current stonepaste potter of Natanz is a quartzite obtained from a quarry (I was able to observe the potter's materials, but he refused to take me to the quarry!). Following Folk (1980) other descriptive terms are used in the full petrographic descriptions (Appendix B), for instance, with regard to extinction.
Another internal feature of the quartz grains that has been recognized and found to be useful, is the cloudiness arising from the presence of fluid inclusions. The degree of cloudiness due to the presence of fine fluid inclusions is given a four-fold division, from optically clear, through slightly cloudy, to cloudy, and finally very cloudy. This is difficult to represent graphically, or even photographically, but the following criteria enable the author to distinguish between the different groups. It must be emphasized that the ultimate point here is to provide this information to petrographers who are attempting to analyse stonepastes, and may already have thin-sections for comparison.
Clear quartz is completely and entirely devoid of any fluid inclusions whatsoever. Slightly cloudy or sub-cloudy quartz will still tend to have some areas clear with a small area of cloudiness, perhaps caused by a single trail or group of inclusions. Cloudy quartz is evenly cloudy, with all parts of the grain being covered by fluid inclusions. The distinction between cloudy and very cloudy is the most problematic. Effectively very cloudy quartz has such large amounts of inclusions that the optical properties of the quartz are interfered with. The relative abundance of each group is estimated as with other minerals. Table 2.2 shows the relative amounts for each petrofabric, including the dominantly clear petrofabrics attributed to Mashhad and Damascus ranging down to the cloudy "Dragon" Petrofabric, found in a distinctive group of fifteenth century ceramics with no known production centre (Mason 1996).
An important consideration is the degree of magnification. Theoretically the higher the magnification, the larger the number of fluid inclusions that would be visible. All the data in Table 2.2 were obtained at 100x magnification. A preliminary study on Turkish "Iznik" style and related ceramics has been initiated by the author using higher magnification (400×) as they are generally of a finer grain size. From this study two petrofabrics are also shown in Table 2.2 ("Ottoman" and Damascus). At higher magnification the "Ottoman" petrofabric appears considerably cloudier, while the Damascus petrofabric is largely the same. Some grains also have distinctively large fluid inclusions. Size of fluid inclusion itself is a variable that has not been utilized by the author as yet. It should also be recognized that the grain size may have an effect on the degree of cloudiness. For instance, a large sub-cloudy grain could be broken down into a clear grain and a sub-cloudy or cloudy grain.
Although not tabulated, another important characteristic of quartz is its extinction under crossed-polars (Folk 1980:65-76). As the crystalline structure of the quartz grain is oriented so that the light is propagated in the same direction as that of the polars, the light should become extinguished. However, under certain circumstances the crystal structure becomes strained, and the "extinction" (the light becomes extinguished) appears undulose. This was traditionally considered to be related to the petrogenetic origin of the quartz but this has been questioned (Blatt and Christie 1963), although more recent work supports such a relationship, especially when combined with data on polycrystalline quartz (Basu et al., 1975). This debate has been avoided here by simply reporting the degree of undulosity. In this study the phenomenon is divided into straight extinction, undulose extinction, and strongly undulose extinction. The distinction between undulose and strongly undulose is here considered to be that strongly undulose grains may contain the full range of extinction within a single grain.
Another characteristic noticed in the quartz incorporated into this material is described as "sheared" quartz in Table 2.2. In cross-polarized light (XPL) this appears as isotropic bands running across the grain. In plane-polarized light (PPL) these bands are often a faint green colour, and adjustment of magnification indicates that one edge of the band is on the top surface of the section while the other edge is on the bottom surface, effectively indicating a narrow "crack" rather than a broad band. However, a simple crack would not produce the phenomenon noted in XPL. Rarely, the "sheared" band is optically discontinuous, and forms classic mylonite mosaics, which are a clear indication of stress. Examination of the literature has not been conclusive. Phenomena such as pseudotachyllitic shearing due to dynometamorphism (Spry 1974) or "slickenslide" development, have been discounted, although both are common along hydrothermal veins, where much of the quartz in this pottery may originate (this is certainly true of Nishapur, where all the fields and streams are filled with dark volcanics and white vein- quartz pebbles). Another possibility that was considered is that the "band" once contained a mineral that may have become glassy during firing. Among more common minerals, both chlorite and calcite are found as late-emplacement veins in quartz veins, and may be destroyed in high-temperature firing. However, such inclusions would show up on the SEM, and this phenomenon has not been observed during that part of the study. Whatever its origin, the presence of this characteristic is consistently related to provenance, and not to any other variable, so it is obviously an important feature to record. "Sheared" quartz is particularly characteristic of the minor late fourteenth century centre at Zahidan, and a group of twelfth to thirteenth century Syrian wares formerly attributed to Raqqa (Raqqa-1, see Table 2.2 and Chapter 5).
In the overwhelming majority of cases, the total amount of quartz given in the cloudiness columns is equal to the total of crystalline quartz. The percentages given for other characteristics (e.g. polycrystalline, "sheared") are generally included under the clear to very cloudy sequence. The "sheared" phenomenon is the one case in which it may be possible to have some quartz not also included under the "degree of cloudiness" columns in Table 2.2, as, although most grains just have a band of the "sheared" appearance, some grains are entirely constituted of "sheared" quartz.
Other inclusions
Many minerals in addition to quartz arecommonly found in fired-clay pottery, but they are less common in stonepastes. Nonetheless such inclusions are very important in the characterization of petrofabrics. When the source material is sand, then inclusion of non-quartz minerals is always possible, indeed, is often likely.
Feldspars are alumino-silicates including potassic members (such as microcline) and the sodic to calcic plagioclase series. Amphiboles are complex groups and series of hydrated ferro- magnesian alumino-silicates. Probably the only amphibole in the pottery covered in this study is hornblende, but the firing process usually alters the optical properties. Pyroxenes are anhydrous calci-ferro-magnesian silicates. In this corpus they are always clinopyroxenes, probably augite, although in some cases there are two varieties. Biotite is a complex hydrous potassic ferro-magnesian alumino-silicate of the mica group, with its molecular arrangement forming platy sheets. Carbonates include the calcium-carbonate calcite and the magnesian- calcium-carbonate dolomite, but these are usually indistinguishable without staining of the thin-section, and may be destroyed by high-temperature firing anyway. Generally, carbonates in thin-section are fragments of limestones. Opaques, mentioned earlier, have not been positively identified but are likely to be iron oxides such as magnetite and haematite, or if derived from basalt may be the titanium-iron oxide ilmenite.
Centres that produced stonepaste containing other minerals include Fustat, where the sand source used contains feldspars and what appears to be a micritic limestone in significant amounts. At Samarqand the sand used contains fragments of feldspar and amphibole from a granitic source, and occasional grains of microgranite. Occasional late pieces from Samarqand (left off Table 2.2) include about 20% of feldspar and 30% microgranite, perhaps indicating problems with this raw material shortly before the pottery failed altogether c. 1450 (Mason et al. 1996). The technically poor-quality Tabriz stonepaste actually contains more non-quartz than quartz inclusions. With regard to the pebble sources, presumably the non-quartz minerals come into the mix as contaminants, perhaps as country-rock attached to quartz veins. The Nishapur stonepaste petrofabric is characterized by inclusion of feldspars of a volcanic origin, often including zoned plagioclase, while the "Ma'arrat" petrofabric from Syria contains cloudy untwinned feldspars.
Polyminerallic grains (those containing more than one mineral type) are petrographically termed lithic inclusions. These may be very important as they more closely represent the rock type from which the grain is derived. Lithic inclusions of coarse-grained rocks such as granite are seldom found, as the grains in the stonepaste are often smaller than the grains in the rock, but occasional very large grains may include these. As mentioned above, the source of the Samarqand stonepaste appears to have been a fine- grained microgranite, as grains containing quartz, feldspars, and amphiboles are found quite often, while in a few cases such inclusions were predominant. More common are the fine-grained volcanic rocks collectively listed under "volcanics" in Table 2.2. These comprise quartz and/or feldspar-rich types, including various types of felsic, acidic, or siliceous chemistry; and also volcanics with a high content of ferro-magnesian minerals, predominantly basalt but including other types with basic or ultra-basic ferro- magnesian chemistry. There is actually a very wide range of textures and chemistries of volcanic rocks, but in thin- section, particularly given the small grains we are dealing with, it is often impossible to be more precise (hence the often simplistic division into "felsic volcanic" and "basalt" in the text descriptions). Examples of petrofabrics with volcanic rock fragments include Nishapur, which contains fragments of a cherty-textured felsic volcanic with small feldspar phenocrysts, and Tabriz, which contains a trachyte- textured felsic volcanic rock with large phenocrysts of feldspars and quartz. Observations of a number of quartz pebbles in the field at Nishapur found dark inclusions, some of which appeared to be of volcanic rock. Fragments of fine-grained metamorphic rock are also found, usually exhibiting banding or foliation.
Grain shape and size
Another important variable is the granulometry of the grains, specifically, their size, their degree of sortedness, and their degrees of roundedness and sphericity.
Grain shape
A grain which is freshly broken or weathered from its original rock is commonly angular. As it is transported and weathered it goes through various stages to become rounded. Comparison charts for estimation of roundedness in sedimentology texts (e.g., Pettijohn et al. 1987, fig. A-2) appear to be generally aimed at providing aid to those characterizing three-dimensional grains in sediment samples rather than two-dimensional grains in thin-sections. The classification used here (see Fig. 2.4) begins with angualr grains, which appear as though freshly broken (it is difficult to see how anything could be "very angular" by this criterion). Subangular grains show some wear on the sharp edges, but are essentially still angular in general shape. A subrounded grain is largely rounded, but still retains some planar fracture or cleavage planes. Rounded grains are completely rounded, with no planar attributes, but may be embayed. Well-rounded grains have no embayments. Sometimes related, but affected by modes of transportation and other factors such as the nature of the grain, is the sphericity of the grain, with a similar range from elongate to spherical.
With clay-bodied ceramics these variables may be entirely dictated by nature, but in the case of stonepaste it may enable the differentiation between the use of sand and river cobbles as a raw material. For instance, most Iranian petrofabrics (Kashan, Nishapur, Mashhad, etc.) are comprised of angular grains, no matter how coarse the grains may be. This is a clear indication that if the original raw material consisted of rounded grains they would have to have been quite large, perhaps even cobbles. This fits well with the description of Iranian potters collecting materials in stream-beds. In the case of Fustat and Damascus, the source was a well-rounded sand, as occasional grains escaped the crushing/grinding process and remain as rounded inclusions within the section. At Samarqand the raw material utilized by the early fifteenth century potters also appears to be a sand, but it is subrounded and mineralogically immature. Documentary and art-historical evidence indicates that potters from Damascus were taken forcibly to Samarqand, where this sand-using strategy seems to have continued (Mason 1996). Abundant quartz pebbles would have been available at Samarqand if it was desired to utilize the standard Iranian pebble-using practice. Rounded grains have been noted in the petrofabric for Rayy, in northern Iran. These grains have carbonate adhering to the outside, which appears to have been a cement in a sandstone. If so, this would fit in well with Ustad ali-Muhammad's description (below) of quartz at Bibi-Shahrbanu being "taken from a hill," as the ridge of this name is next to the ancient site of Rayy. Although I have not visited the site myself, there is presently a glass factory at the site using local raw materials.
Grain size
Unless subjected to processing the size of a grain is related to the degree of weathering and erosion it has been subjected to, while its collection into a raw material deposit that can be utilized is dictated by the environment in which it was deposited. A slow-moving and meandering river is more likely to deposit fine sands and silt, a high-energy beach deposits well-rounded mature sands, and a swiftly moving mountain river is more likely to deposit cobbles and coarse immature sands. The grain size of the original raw material is not always evident in stonepaste thin-sections, but where sand is used and the original grains were not all crushed, an important variable is preserved for recording. For example, the sand used at Fustat is about 1 mm diameter, while that at Damascus is about 0.3 mm diameter. With regard to the pebble-source petrofabrics it is unknown precisely what dictates the often distinctive grainsize distribution for a site, but it is difficult to imagine that the result of breaking, crushing, grinding, and sieving could be other than entirely dictated by human agency, and not geographical determination. Hence the distinctive grainsize distribution profile for each site may just be an expression of the tradition of a particular centre.
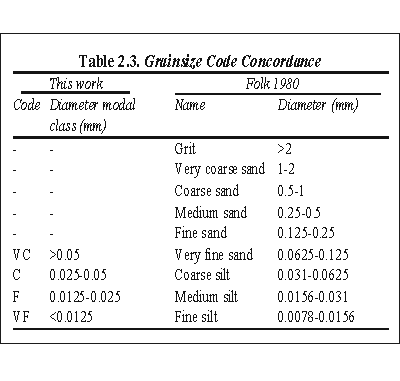
Grainsize distribution is recorded by counting about 150 grains in a ribbon-shaped sample of the thin-section observed in this study at 100× magnification, and recalculating this to 100%; distribution therefore expresses the proportion of grains of a certain size in relation to the total number of grains, not to the entire body as in the percentage of mineral abundance. This method was developed and tested specifically for use in archaeological ceramics by Andrew Middleton and colleagues at the British Museum (Middleton et al. 1985). The data are then shown as a histogram in which grainsize values for the different minerals are kept separate. The histograms give a rough idea of the relative proportion of each mineral, but are only for grainsize analysis and should not be considered to be as accurate as the values provided for mineral abundance. This is especially so of stonepastes, as the non-quartz inclusions tend to be a smaller proportion of the total count of grains than they do in clay- bodied wares. Some other workers do not record the finest grain sizes, which are smaller than the thickness of the thin-section (0.03 mm). Although it is recognized that this value is unreliable in clay ceramics, this is no excuse to ignore the fraction altogether, and in stonepaste ceramics with glassy matrices all grains tend to be visible. Figure 2.5 shows a selection of grainsize-distribution histograms of stonepaste ceramics not otherwise discussed in the present study (see Mason 1996). In Table 2.2 a code for the grainsize modal class is given (VF, F, C, and VC), and these codes refer to the maximum grainsize column in the histograms. For instance, "VF" (very fine) refers to a histogram in which the modal class is under 0.0125 mm diameter (e.g., "Ottoman" Petrofabric). Subsequently "F" (fine) equals 0.0125 to 0.025 mm diameter(e.g., Nishapur Petrofabric), "C" (coarse) equals 0.025 to 0.05 mm diameter (e.g., Samarqand(?) "Syrian Blossom" Petrofabric), and "VC" (very coarse) has a modal class greater than 0.05 mm diameter. This does not correspond closely with widely recognized sedimentological terms for grain sizes provided in Table 2.3 and also used throughout this work (see Folk 1980).
The grainsize-distribution histogram for the Samarqand(?) Petrofabric (see Fig. 2.5) shows the rounded grains as a separate category. For most production centres it would appear that pebbles or other coarse material was all that was available. In most centres a remarkable consistency of grainsize distribution appears to have developed. Although the basic method of crushing the quartz appears to have been largely similar throughout the Islamic world, each centre tended to have a largely unvarying grainsize profile, for instance, note the distinction between Raqqa-1 and "Ma'arrat" in Figure 5.11. Both centres are Syrian and of twelfth-century date, and contain no rounded grains, not even a rounded facet on the occasional stray large grain. Hence, these were presumably pebble quartz sources, but their grainsize distributions are distinct. This narrow range of variability is found in the other petrofabrics, often in each case distinct from profiles of other centres. That this is indeed a cultural attribute is underlined by the existence of two separate grainsize profiles for the same centre. At both Nishapur and Samarqand in the fifteenth century there appears to have been an effort to make the aesthetically finer wares using finer-grained quartz (Mason 1996). In the case of the Samarqand pottery the "finer" wares, called the "Phoenix" group after a distinctive decoration, also received a tin- opacified glaze, unlike the normal clear alkali glaze of the "coarse" wares, known as the "Syrian-Blossom" group. This would fit in well with Ustad Ali Mohammad's admonition (below) to grind quartz fine: "the finer the better." Although this does appear to be a cultural attribute, granulometric analysis is still worth undertaking, as each site may be distinguished by it, and within a site it will provide information on differences in processing, which may reflect the practices of different workshops. In the case of clay- bodied wares it provides an essential component to characterization, especially in regions such as the Tigris-Euphrates basin.
Degree of sorting
Another criterion used to estimate the "maturity" of a sediment is its degree of sorting. Although sedimentologists use very closely defined parameters in their definitions, this may be simplistically described as meaning that a "sorted" fabric has grains of more-or-less the same size, while an "unsorted" fabric comprises grains of a diversity of sizes. The actual terms as defined by sedimentologists (very well sorted, well sorted, moderately sorted, and poorly sorted) refer to rigidly defined parameters, but acceptable comparison charts are available (e.g., Pettijohn et al. 1987, fig. A-1). However, these are again specific to grain-packed sandstones, and I have constructed a matrix-dominated version more useful to archaeological ceramic petrologists (Fig. 2.6). As with grain size, it is unclear what produces differences in sorting of stonepaste ceramics, but among clay-bodied wares it is an important geographically dependent variable.
Petrography method discussion
Petrography, as we have seen, provides a large set of geographically related variables. The mineralogy and lithology of the grains is dictated by the geology of the region from which the grains are derived, and their shape, size, and sortedness is dictated by the geomorphology and depositional environment of the raw materials utilized by the potter. Although processing must be responsible for a certain amount of the variability found in these ceramics, it is the availability of raw materials that essentially dictates what will appear in thin-section.
The infinite hypothetical variety of petrofabrics allowed by these variables is contrasted by the finite, and often very restricted number of actual production centres represented by the material studied here. Hence, the preferred focus is the characterization of the products of centres, by analysis of kiln evidence such as ceramic kiln furniture and wasters. Kiln furniture in Islamic contexts is found most often in the form of kiln-trivets, used to stack pieces on top of each other; kiln-rods that projected from the side of the kiln and upon which the vessel rested; or, in some areas and periods, saggars, ceramic boxes which contained the glazed vessel. Wasters are pottery pieces that were damaged in firing, were consequently entirely useless, and were immediately discarded. Where such damage is subtle, it must be supported by the ceramic type being found in significant numbers in close proximity to a contemporary kiln. The practice of potters also trading in the products of other centres should make one wary even of this. I have observed such practices at al-Jerahi, near Zabid in the Yemen, and to a greater extent by a family of potters at Shahreza near Isfahan in Iran. Interestingly enough, the latter group had a large pile of broken pottery, including wares from Maybud and Hamadan, right next to the kiln. The wasters that are preferred for analysis comprise completely collapsed vessels, or several vessels fused together, or others which are obviously and self-evidently useless. Pieces that are slightly warped or scarred by other pieces can at best be considered "seconds," and could have travelled far from the kiln. Other undesirables include sherds from excavation that appear burnt, an occurrence that could happen in any fire. Given the almost infinite variability that may exist if one considers geological sources, and also given the possibility of the movement of raw materials, this approach of defining the actual products of these centres is considered by far the most reliable.
Stonepaste petrofabrics and raw materials
A large body of ethnographic work has been undertaken on the procurement of clay by potters, and it has thus been possible to make valid general statements. The only full ethnographic account of a stonepaste pottery is the study by Centlivres- Demont (1971), on the potters of Maybud, 60 km northwest of Yazd, Iran. The town of Maybud is situated on a high-altitude oasis at the edge of the Dasht-i Lut desert, and ceramic production was restricted to the spring and autumn. Glazed and unglazed fired-clay ceramics, as well as stonepaste, were made in the town. Of over twenty workshops, each employing one to four potters, six workshops of one to two potters each solely produced stonepaste. The quartz was obtained from mountains 24 km to the west, and is described as being white, shiny, and in lentil-sized grains. This was then crushed in a mill. Although the archaeological pertinence of observations regarding transportation, milling, and kiln fuel are rendered suspect by the introduction of petroleum-fuelled devices, the stonepaste potters used fuel that is twice as expensive as that used by the clay potters, so as to achieve higher firing temperatures. Consequently, the stonepaste vessels were three times the price of similar clay wares upon completion. The pieces were sold through Yazdi shopkeepers, and were from then on known as products of Yazd. The Yazdis marketed them over a wide area by the bus system.
Wulff (1966:151-67) gives a thorough description of the practice of stonepaste potters (sangineh-saz) of Isfahan, Natanz, Kashan, and Qum, whose products are mostly sold to the pilgrims at the shrine of Fatima in Qum. What Wulff describes as flint (sang-e chahmaq) and quartz are collected in dry river beds, unless there is a good quarry nearby, as at Natanz (the product of which I have observed to be quartzite). Although the collectors can distinguish between quartz, limestone, and gypsum, the cobbles are brought back to the workshop for final separation and crushing, where the quartz is sorted out. Particularly white pieces are set aside for glaze-making. Pebbles are first crushed with an iron bar, then pounded in a basalt mortar to grit size, and finally ground yet finer in a wet hand mill. The body is then made using 70-80% quartz, 10-20% fine clay, and 10% glass. The paste is rather stiff, and vessels tend to be thrown in two or more parts, and then fixed together. The formed vessel may then be covered in a "slip" of 90% extremely finely ground white quartz, 7-9% fine clay, and about 1% tragacanth gum.
In the 1880s the master potter Ustad Ali Mohammad, a native of Isfahan, described his procedure, which was written down by a scribe and translated into English (Mohammed 1904). His quartz is called seng-i-chekhmaq, which the translator considers to be a kind of flint. This material is found at Isfahan (from the bed of the river), and is also found near Na'in, Ardestan (described as "the best of all places"), Qum, and near Tehran at Bibi-Shahrbanu (where it is described as "in a hill," presumably referring to a quarry). The quartz is broken up with a hammer, sieved, crushed and put through a mill "till it becomes fine—the finer the better." The powdered quartz is then added to clay, from Vartoon near Isfahan, and glass at a ratio of 8:1:1.
The treatise of Abu ‘l-Qasim, dated to 1301, also provides an account of raw material procurement and ceramic technology (Allan 1973a). Abu ‘l-Qasim's quartz is called shukar-i sang, literally meaning "sugary stone," an evocative name for quartz, which is very similar to the sugar blocks available to Abu ‘l-Qasim. He describes it thus: "It is a white, clear, shiny stone, less clear than rock crystal, but clearer than white marble. It is very hard, and many sparks come off it by means of the fire iron. Its deposits are in many places."
With regard to processing of the quartz, he states: "to compound a body out of which to make pottery objects . . . take ten parts of the afore-mentioned white shukar-i sang, ground and sieved through coarse silk, and one part of ground glass frit mixed together and one part of white Luri clay dissolved in water."
A further Iranian source is found in the account of Jean Chardin, who travelled in Iran between 1673 and 1677 (Chardin 1988:267-68). Chardin considered pottery, or at least the fine stonepaste wares that he refers to as "Enamel," as one of the principal crafts that "the Persians understand best." With regard to production centres, Chardin writes: "The Enamel Ware . . . they make all over Persia." However "the finest" is made at Shiraz, Mashhad, Yazd, Kerman, "and especially in" Zarand. Chardin also mentions the potters of Isfahan, but it is unclear what materials their bodies comprise. Of technology, Chardin gives an effective though brief description of stonepaste: "The Matter of that fine Enamel is glass, and little River Pebbles pounded very small, together with a little Mould mixed in."
Only one source appears to refer specifically to sand as a source of quartz. This is the account of John Covel, describing the raw materials used by the Iznik potters in 1677 (Atasoy and Raby 1989:50-51). Covel describes "excellent white sand about 6 or 8 miles out of town."
Accounts for the royal tile workshop of sixteenth-century Istanbul also provide some significant observations (Necipoglu 1990). The workshop itself appears to have consisted of at least five kilns, and had mortars, equipment for melting ingredients, and a water tank into which the melted ingredients were poured to shatter into small fragments. These accounts indicate that certain materials (clay, potash, limestone, wood) were certainly brought in by boat. However, the costs for several hundred pieces of kit'a (interpreted as being quartz), ten baskets of stone (küfeh -i seng), and one piece of seng-i çakmak (interpreted as "flintstone") do not seem to include freight costs (Necipoglu 1990, Appendix 1). The use of the terms kit'a and ‘adad, interpreted as meaning "pieces", would seem to indicate that this centre was not using sand, which would, most likely, be referred to as being shipped in a container.
Apart from the last two, all of these sources refer to Iranian practice, but are probably applicable to any area of high relief in the Islamic world, where sand would be too immature (i.e., it contains too many non-quartz grains) to use. Where the writer is specific, the majority of sources appear to be alluvial gravels. These would comprise cobbles of vein quartz or chert, weathered from their original host rock, probably with some host-rock cobbles (the host rock of a quartz vein or chert would probably be more susceptible to weathering than the quartz). Quarries and other sources may represent in situ vein quartz, but are more likely to indicate an ancient deposit of mature sediments, such as quartzite or an indurated sandstone.
Although gravel deposits are relatively common, it must be assumed that those which are sufficiently quartzose while being large and reliable enough to support a number of workshops for a century or more must be conspicuously rarer. When potters came into a new area to establish a workshop, the abundance of various raw materials, especially a dependable source of quartz, would have been an important consideration. The source would probably be homogeneous, and would therefore explain the well-defined petrofabrics for each kiln site. However, a possibly even greater control is the geographic scale and ecology of the Middle East. Coming from a country in which it is possible to set up a pottery every few hundred metres, it was rather staggering for me to find when driving through Iran that there are tens of kilometres distance between viable habitation sites. Useful raw materials may be quite common, but if it is possible to live only in the occasional oasis, like Kashan or Isfahan, then only the raw materials that occur within reasonable distance of that site can be of use. Hence, a picture of a complex of workshops in a single town relying solely on one large and dependable source of quartz is probably accurate in most cases for the majority of the time.
Centlivres-Demont describes a journey of 24 km to obtain quartz. If this was the centre of an area across which the potters ranged, going to one valley on a certain day, and another valley the next day, then it would probably be impossible to define the products of a particular site by petrography. But what is clearly described in the sources is not aimless exploration for raw materials, which would be a waste of time and effort, but the return to a single reliable source. Although aimless exploration for quartz sources appears unlikely, given the scale of production of Islamic ceramics, the possibility of the long-distance movement of raw materials can not be dismissed. With clay ceramics we have large numbers of ethnographic accounts arguing against this hypothesis, but with stonepaste we only have Centlivres-Demont's account of 24 km for Maybud, and Covell's account of six to eight miles (c. 11 km) for Iznik. The modern Maybud potters may not be a good model, as they are able to fetch the materials in pick-up trucks. If the royal tileries at Istanbul were bringing quartz in by boat, it may have travelled some distance, but this may be a unique example. Most production centres for stonepaste-bodied wares are distant from each other, as stonepaste was a technologically demanding material, not produced in every village or town. Such distances would even dwarf the ability to move raw materials that existed in Europe during the industrial revolution. Even where centres are relatively close, for instance, Mashhad and Nishapur are about 75 km apart, it has proven possible to define different, or in this case radically different, petrofabrics (see Table 2.2; cf. Mason 1996). By driving between the two cities it is equally obvious that no one is seriously going to set up a rival centre in between that might or might not mix the two sources of raw materials.
Even if the theoretical movement of raw materials were possible, the problem this would present to characterization is obviated by the preferred strategy of characterization by analysis of wasters, kiln furniture, and other evidence, which will link a petrofabric to a particular centre regardless of the origin of the raw materials. The successful petrographic characterization of production centres strongly supports the effectiveness of the above criteria. In no case has it been shown that one site has produced more than one stonepaste petrofabric, unless this dichotomy has been obtained by differences in processing. Where wasters have been analysed in significant numbers (such as for the "Ma'arrat" Petrofabric, where most of the twenty-five samples were wasters) they have always comprised a single consistent petrofabric. Further, the petrographic groupings consistently agree with major typological groupings, enabling the attribution of distinctive ceramic styles to production centres. This is even true of wares in which typological groupings were previously poorly defined, for it has generally proved possible to define stylistic and other typological criteria for certain centres based on study of pieces attributed by petrography.
The petrofabrics
All samples that have the same petrography, and can be distinguished petrographically from other groups of samples, are grouped together into a petrofabric. In those cases in which wasters from a particular site are included, then that petrofabric is considered to have originated at that site. These petrofabrics are named after the site, for example, the Basra Petrofabric. In some cases tentative attributions are made on reasonable evidence. Tentative attributions have the place name followed by a question mark in parentheses, for instance, the Damascus(?) Petrofabric. These attributions are generally reasonably secure, and in some cases certain (such as the given example).
Petrofabrics that can not be reasonably attributed to a production centre are named after the site where they were first defined, hence the "Siraf" and "Samarra" Petrofabrics are not necessarily thought to have been made at these sites. Often a number of petrofabrics will be defined from analysis of pottery from a particular site. In these cases they are numbered in sequence (e.g., "Samarra 3" or "Siraf 2"). An unbroken sequence of numbers should not necessarily be expected in this study for two reasons. Firstly, the petrofabric may have already been defined at another site and so the previously studied site will have precedence (e.g., "Siraf 8" was previously defined as "Samarra 2" and is so reported here). Secondly, the petrofabric may have either previously or subsequently been attributed to a kiln site, which will also have precedence (e.g. "Samarra 1" was later elevated to Basra Petrofabric). In some cases petrofabrics are defined by analysis of pottery which was not obtained from archaeological sites, and in these cases some other name is invented, based on either decorative motif or art-historical nomenclature (e.g., "Tell Minis" petrofabric). In one case what was previously considered to be a reliably attributed petrofabric has subsequently been shown not to be so: that formerly known as the Raqqa Petrofabric (see Chapter 5).
In all cases the possibility that petrofabrics may be geologically compatible is examined, in case they are variants from a single centre. This has particularly been the case with petrofabrics unique to single samples, as their infrequency may be indicative of their position as anomalies. Certainly centres have been known to have more than one clay petrofabric, usually different quality clays being used for vessels with different functions. Furthermore, it is acceptable to have a stonepaste and a clay petrofabric having the same origin, as described for Maybud, as the two types would have been made for different markets. Indeed, wasters of late fourteenth century pottery from Zahidan include vessels of clay and stonepaste bodies fused together (Mason 1996).
SCANNING ELECTRON MICROSCOPY
The investigation of the technology of production of the studied material was primarily undertaken using a scanning electron microscope (SEM) with attached analytical facilities. This technique has become the standard approach to unravelling technological questions regarding ceramic technology (Freestone 1982, Tite 1992), particularly in the study of glazes, where chemical weathering and consequent structural decay of the surface makes other analytical techniques unsatisfactory. The technique has been applied to various Islamic ceramic types, including some further analysed in this study (Kleinmann 1986; Tite 1988).
An SEM uses electrons in much the same way as ordinary microscopes use light, bombarding the sample with the sub-atomic particles, and then collecting the reflected electrons (secondary electrons), or the electrons emitted by the bombarded sample (backscattered electrons) to develop an image (see Fig. 2.7). As electrons are very much finer than the wavelength of light, an SEM can produce images of much higher resolution than light microscopes. Secondary electrons can be used to develop an image of the topography of the sample, for instance, wear patterns on lithics, or to enable identification of organic remains. Images produced by backscattered electrons provide information about the chemical structure of the sample, as the degree of intensity of the electrons is proportional to the atomic number of the element in the sample. For example, something containing a high proportion of lead will appear much brighter than an inclusion of quartz. For this analysis a polished section is made from the sample, and it is thereby possible to investigate the texture and relationships of the different components of the material being investigated.
The X-ray spectrometer bombards a small area, as small as a few microns, of the preferably polished sample with an intense electron beam (see Fig. 2.7). The sample then emits X-rays of a wavelength characteristic of the elements in the material at an intensity related to the proportion of that element. As a result, it is possible to determine the chemistry of very small areas, for instance, the grains of pigment in glazes and glass, or the metallic crystals within an alloy. This method may also be used to examine parts of the ceramic body, to obtain, for instance, chemical data for the clay matrix of the ceramic, rather than the whole body, which may be altered by tempering, or the glassy interstices of quartzose bodies like so-called Egyptian faience. By using a more diffuse beam it is possible to obtain bulk chemical data of ceramic bodies, glazes, glass, and metals.
Procedure
Preliminary examination of glazes and bodies was first undertaken using a 10× to 40× binocular zoom optical microscope and then, in thin-section using a polarizing microscope. In this way it was possible to obtain limited technological data on a much larger number of glazes than was possible using the SEM. Polished sections of the samples were made, including the body and the glazes of the interior and exterior of the vessel. These were examined in the SEM (Cameca SEMprobe) using a backscattered electron detector (BSE mode), with which it was possible to distinguish the phases present on the basis of the differences in their atomic numbers, which are revealed by different shades of grey (e.g., quartz appears darker than the higher atomic number glaze and glass phases). The chemical compositions of the glaze, body, and other components were determined using an attached energy-dispersive X-ray spectrometer (EDS) and a wavelength- dispersive X-ray spectrometer (WDS).
Initial analysis was done using EDS operating at 20kV and current of 10nA, with a 100 second count. As adjacent spectral peaks of potassium may lead to spurious tin results (i.e., up to 4% nonexistent SnO2; see also Henderson 1988 for discussion of the relevant literature), tin was analysed at that time with WDS. Lead was also analysed using WDS, again in order to avoid spurious results (up to 1% nonexistent PbO) and thus to distinguish conclusively between leaded and unleaded glazes.
Individual EDS analyses sampled as large a field as possible within the area of the feature to be analysed, up to a maximum of 2.5 × 1.5 mm. The area of glaze sampled for analysis was slightly less than the glaze thickness and typically in the range 110 × 90 up to 900 × 700 . Any weathered or contaminated surface layer and the glaze-body interface were avoided, as was any major inhomogeneity, such as an inclusion as large as the glaze thickness. However, typical more evenly distributed inclusions, such as tin oxide particles, were necessarily included. Normally a minimum of two analyses were made on each glaze and these were then averaged. Due to pores in the glaze, the analytical totals were typically in the range 90- 95%. Because of the inhomogeneities in many of the glazes, analyses of the same glaze could differ by as much as ±4% absolute for major elements (i.e., SiO2, PbO) and by as much as ±10% relative for the minor elements. However, when the glazes were homogeneous, analysis of the same glaze was reproducible to less than ±1% absolute for the major elements and less than ±5% relative for the minor elements. Analyses of bodies typically produced a total of about 65%, and so should not be considered fully quantitive. Detection limits were generally thought to be about 0.2%, although magnesium may have a limit of up to 1%, higher in the presence of alumina; lead and sodium had a limit of 0.5% (the limit for lead would be higher in the presence of sulphur), and tin had a limit of up to 1%, higher in the presence of potassium.
Unacceptable errors for some elements in some glazes were eventually recognized in the EDS system, and many of the glaze analyses were redone using WDS. Operating conditions were 20kV and 10nA with count times of 10 seconds on peak, 5 seconds on background either side. However, if the count rates were low, these times may have been doubled or trebled. Analyses were typically undertaken at a magnification of 4000× which gives an analytical area of about 30 × 40 . Under these conditions, the detection limits should be typically 0.01 to 0.05 weight per cent, and precision would be 1% or better assuming good carbon coat. Accuracy is element dependent with sodium easily being as much as 5-10 % relative low, most other elements would be within the 2% relative range, with the proviso that the analytical volume was uniform, large errors could arise with a distribution of small silicon- or aluminium-rich particles (3% and below). Typically more than five analyses were made if sufficient surface area was available. Although this appears to provide a satisfactory result for elements evenly distributed throughout the material being analysed, total for tin oxide may be suspect, a problem that would require several days' analysis per sample to rectify. The tabulated data is presented within the main text as a standardized total.
SYNTHESIS
The following chapters will present the results of research undertaken in each of these three areas, and then the three strands of when, how, and where will be brought together to form a synthetic whole. In this way the significance of each finding will be augmented by correlation with findings in the other areas. For instance, to fully understand the relevance of the technological findings to the history of ceramic technology, it is essential that they be put in a chronological framework.
Return to Table of Contents
|